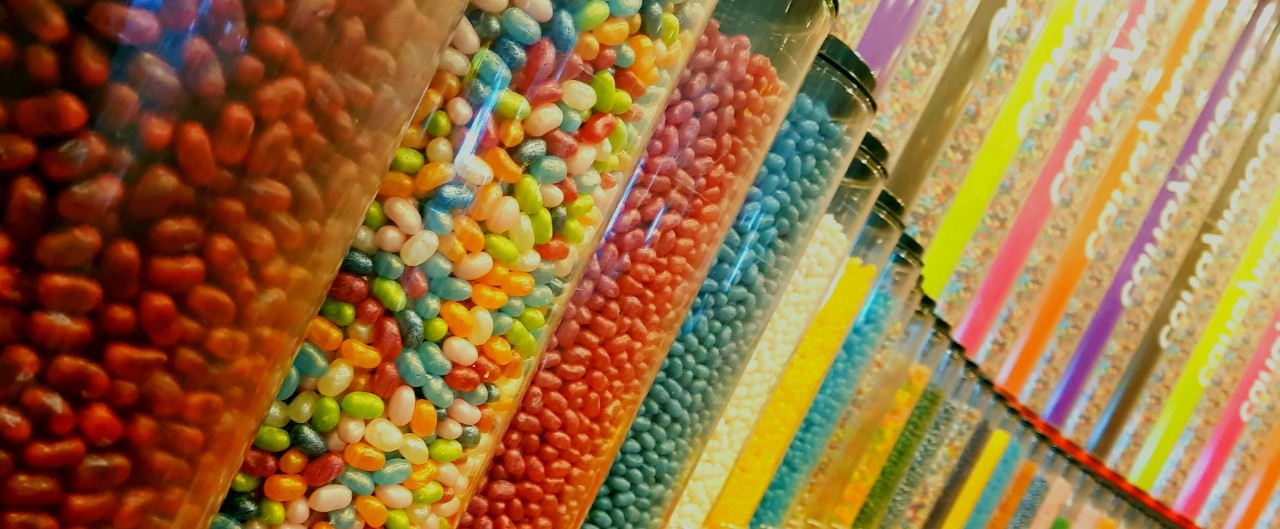
Depuis plus de 50 ans, USC Consulting Group (USCCG) encourage l'excellence opérationnelle en ayant pour mission de fournir une réelle valeur grâce à l'amélioration des performances financières. USCCG aide les entreprises à atteindre leur plein potentiel en améliorant les procédés et les opérations dans l'ensemble de leur chaîne d'approvisionnement. Les solutions Minitab apportent une aide essentielle à USCCG dans la résolution des problèmes de ses clients tout en permettant la poursuite de ses opérations à des niveaux optimaux.
Le défi
Si vous travaillez dans le remplissage d'emballages, vous savez à quel point le contrôle des procédés de remplissage est important. Les conséquences d'un trop-plein ? Vous donnez tout bonnement de l'argent à vos clients. Dans le cadre d'opérations à gros volumes, ce phénomène peut rapidement revenir à des centaines de milliers de dollars par an. En revanche, si votre emballage ne contient pas assez de produit, les amendes et l'impact sur votre réputation peuvent s'avérer encore plus coûteux.
Lors du remplissage, l'exigence première est de répondre aux réglementations gouvernementales pour être en conformité avec les déclarations de contenu net des produits emballés. Autrement dit, le poids de remplissage unitaire du produit doit dépasser une valeur minimale définie, conformément à la variation maximale autorisée (MAV). Le poids moyen de remplissage doit être égal ou supérieur, jamais inférieur, à la mention figurant sur l'étiquette.
De nos jours, de nombreuses entreprises pensent que le trop-plein est la seule manière d'éviter les amendes et de conserver la fidélité des clients. Ainsi, leur but est de se rapprocher le plus possible du poids d'emballage déclaré sans aller en dessous. Cette technique semble parfaitement raisonnable, mais beaucoup d'entreprises ont du mal à atteindre cet objectif. La raison se trouve-t-elle dans le fait qu'elles ne comprennent pas complètement leur capabilité de procédé ? Ou alors, n'ont-elles pas adopté les outils et techniques adaptés, comme Lean, Six Sigma ou des solutions technologiques, afin de réduire les variations et de contrôler les procédés ? Il s'agit peut-être simplement d'un souci d'exécution. La réponse se trouve dans tout ou partie de ces éléments.
La minimisation et le contrôle de la variation du poids de remplissage associés à une modélisation statistique peuvent vous permettre d'augmenter considérablement vos bénéfices nets. Minitab est la solution idéale pour optimiser le poids de remplissage et a aidé des clients de différents secteurs à réduire l'équivalent de millions de dollars de trop-plein.
Comment Minitab a aidé
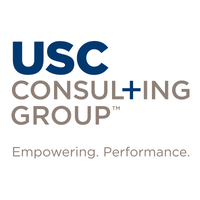
L'Organisation
- Société de conseil en gestion des opérations spécialisée dans l'amélioration des procédés.
- Siège social à Tampa en Floride
- Environ 200 employés
Le Défi
Lors du remplissage, l'exigence première est de répondre aux réglementations gouvernementales pour être en conformité avec les déclarations de contenu net des produits emballés. Le poids de remplissage unitaire doit dépasser une valeur minimale définie, et le poids de remplissage moyen doit être égal ou supérieur, jamais inférieur, à la mention de l'étiquette.
Produits Utilisés
Minitab® Statistical Software
Resultats
- Le trop-plein pour les bonbons emballés a été réduit de plus de 50 %.
- Economie annuelle de plus de 1,2 million de dollars sur les matériaux.